Direct Drive BLDC Motors for Cooling Tower
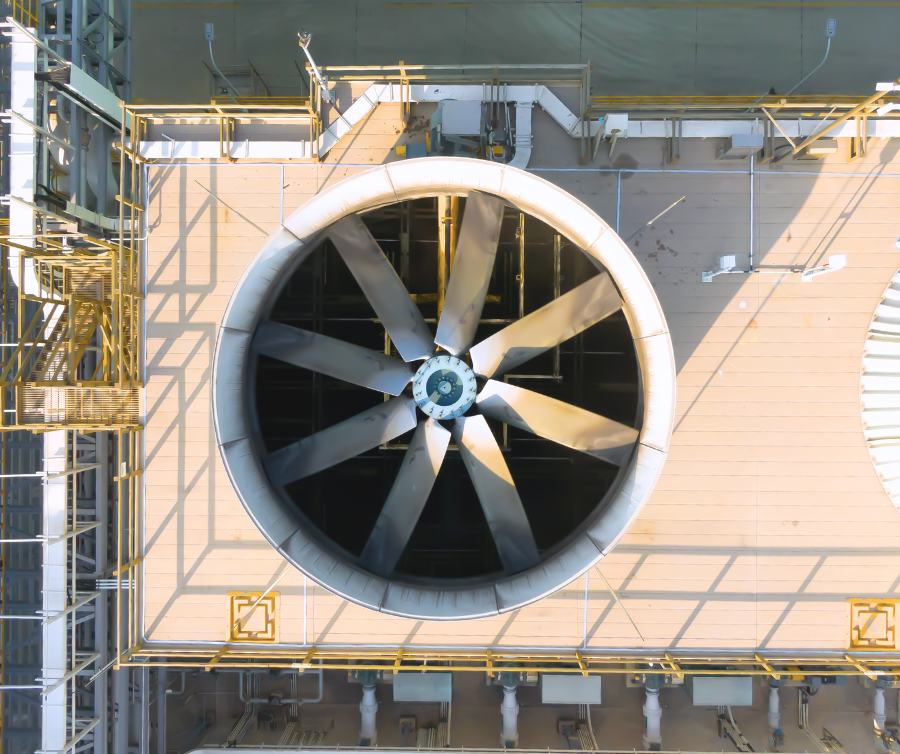
Innotec’s innovative approach combines advanced technologies to create high-performance direct drive BLDC motors for cooling tower applications. Pairing the proven permanent magnet (PM) designs with an adjustable speed drive, our solution delivers exceptional torque without the need for traditional gearboxes or belts. By directly coupling the fan to the motor and controlling it with a specialized AC drive, we optimize speed and cooling tower efficiency while reducing noise and energy consumption. Working with Innotec, gives OEMs the opportunity to change mechanical and electrical features of their motor specifications.
We have a wide range of standard BLDC motor offerings for Cooling tower applications:
How Direct Drive Motors increase efficiency?
Innotec’s Permanent Magnet Synchronous Motor utilizes a Brushless design with naturally heat dissipating finned Aluminium frame construction, delivering a power-dense, highly efficient package with flange mounting dimensions. This design adeptly replaces the conventional installation of right angle gearboxes and jack shafts in cooling towers. This setup not only enhances energy efficiency but also minimizes maintenance requirements by eliminating complex intermediary components prone to wear and tear.
Moreover, the direct drive system with a Brushless PMSM provides superior speed control and torque capabilities without sacrificing efficiency, allowing for precise adjustments for specific cooling demands in cooling tower industrial settings. Built upon strong permanent magnet technology designed for tough industrial settings, these PMSMs are perfect for handling the tough, hot, and humid conditions within the cooling tower. The bearings, engineered for environmental resilience, provide operational stability, effectively safeguarding the motor against dust and contaminants. The inherent characteristics of the Brushless motor, coupled with the direct drive setup, result in an efficient, low-maintenance solution that maximizes performance while minimizing energy consumption and operational complexities compared to traditional induction motors with gearboxes and shafts for cooling towers.
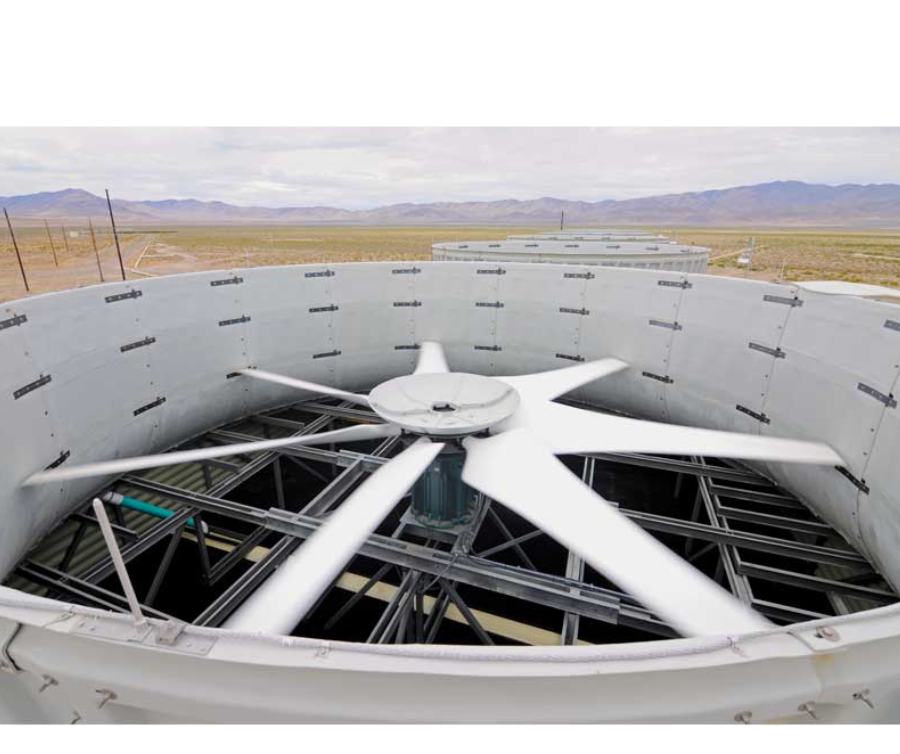
Integration with existing VFD
Designed to integrate with existing Variable Frequency Drives (VFDs) commonly employed with traditional Induction motors, these PMSMs stand out for their better performance and higher efficiency. This universal integration of our PMSMs with the VFDs enables precise speed control, optimizing energy consumption and enhancing operational efficiency, eliminating the need for extensive system overhauls. These VFDs enable gradual acceleration and deceleration of the motor, reducing mechanical stress on the system and prolonging the motor’s lifespan. The motor operates at the necessary speed without wasting excess energy. In cooling tower applications, where varying loads are common, this can lead to significant energy savings.
Heat management
Engineered with a finned Aluminum frame design, our PMSMs integrate natural cooling principals and even during prolonged operations they exhibit exceptional thermal control, maintaining temperatures within optimal ranges. By effectively dissipating heat and preventing excessive temperature buildup, these motors maximize efficiency, a critical factor in their exceptional performance within cooling towers’ demanding operational landscapes.
Testing and Reliability
To ensure the reliability and endurance each unit is lab tested in our facility. Talking about our most efficient one, we subjected the 255-DZ48-080 BLDC motor through its paces with maximum current settings at 80 Arms, 120 Arms, 160 Arms and 240 Arms. Even under these demanding conditions, the motor exhibited resilience, with maximum temperatures reaching just 78 degrees, 86 degrees, 112 degrees and 123 degrees Celsius during one-hour continuous testing.
Energy Saving Optimization
Significant energy savings can be achieved by optimizing the motor speed. Designing the entire cooling tower system to accommodate the ‘Worst Case’ scenario, which involves the highest air flow, is essential. Achieving optimal system performance might necessitate running the fan at a reduced speed.
When the motor speed decreases, the air flow diminishes in a directly proportional manner. For instance, if the motor operates at just 50% speed, the air flow also decreases to 50% of the maximum air flow.
However, the power input to the motor fluctuates exponentially with the cube of the motor speed. For instance, when a motor runs at half-speed, the power consumed is only 12.5% or 1/8 (i.e., (½)3) of the power consumed at full speed. Hence, if the required airflow can be attained by operating at half-speed, there’s potential for substantial energy conservation.
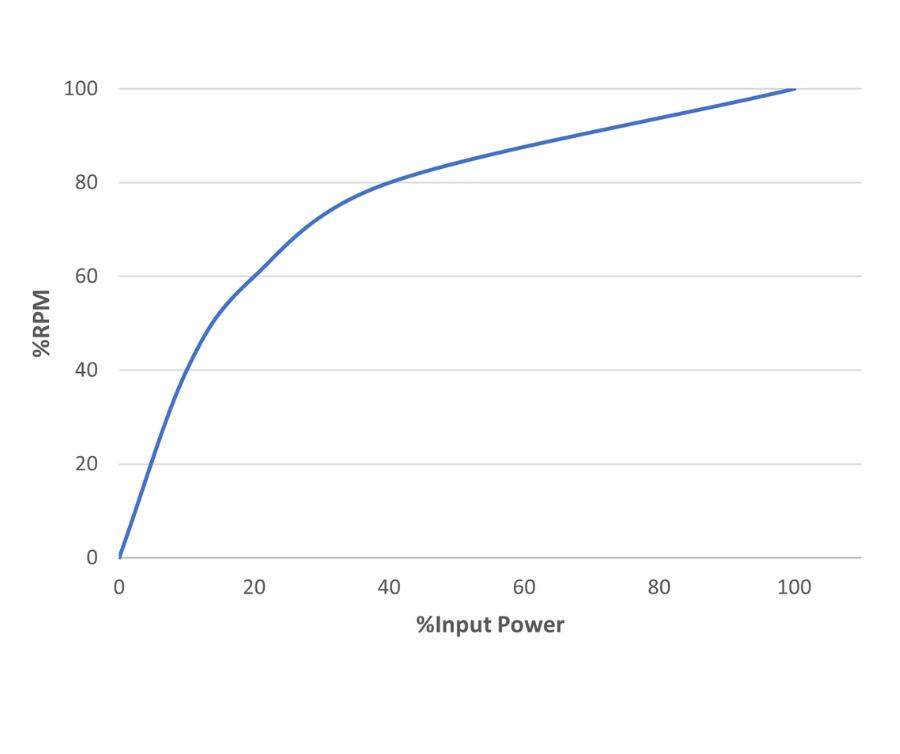
Features & Benefits of Direct Drive Cooling Tower Motors
- Reduced Maintenance & Enhanced Reliability: Direct drive motors minimize maintenance, ensuring reliable long-term operation.
- Efficient Installation & Cost Savings: Simplified installation without any new aligning components reduces costs and boosts system efficiency.
- Improved Safety: Eliminating rotating parts enhances operational safety in the environment.
- High Power to Weight ratio: High Power output in a compact form factor.
- Fault-Free Operation: No gearbox oil or leaks, ensuring an eco-friendly operation.
- Simplified Structure: Removal of gearboxes, shafts, bearings, and couplings streamlines the system’s design and maintenance.
- Sealed Design for Harsh Environments: Offering different level of ingress protection (IP) ratings depending upon site conditions.
- Optimized Energy Use: Direct drive motors are highly efficient, reducing overall power consumption for cost savings.
- Reduced Transportation cost: The weight reduction in each unit can impact results in lower transportation cost.
- Peak Torque Across Wide RPMs: The motor achieves peak torque values across a broader spectrum of RPM, enhancing its operational flexibility and performance at varying speeds.