Inverter Motor & Variable Frequency Drive
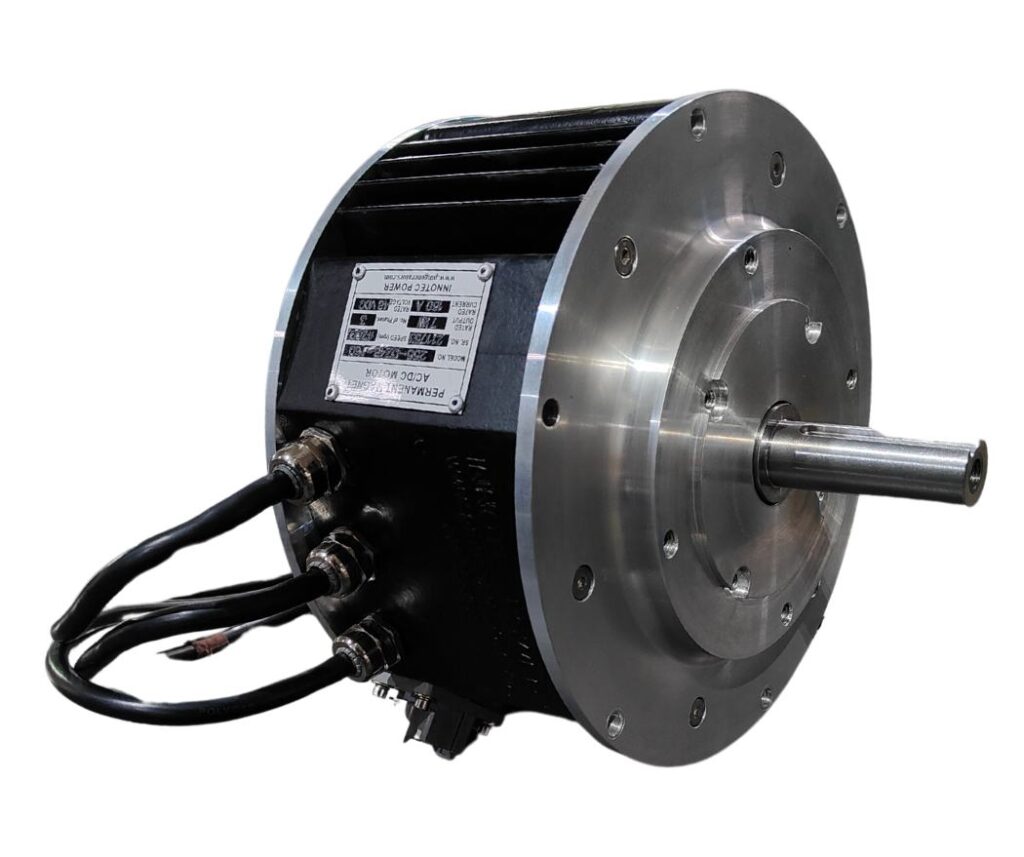
An Inverter Motor refers to an Electric motor that operates with the help of an Inverter or a Variable frequency drive to control its speed and torque. This is why they are also known as variable frequency drive (VFD) motors or adjustable speed drive (ASD) motors. Usually a traditional electric motor operates at a constant speed depending upon the frequency of current supplied, but the Inverter motor uses an electronic device called VFD controller to vary the frequency. By adjusting the output frequency, VFDs can match the motor speed to the specific requirements of a task, reducing energy consumption during periods of low demand and extending equipment lifespan.This flexibility in speed control makes inverter motors suitable for various applications like Electric & Hybrid Vehicles, Material Handling, Industrial automation, Defence & Military, etc. Inverter motors not only enhance overall system performance but also contribute to substantial energy savings.
Types of Inverter Motors:
- Induction Motors with VFD:
These motors are designed to work with Variable Frequency Drives (VFDs) to enable variable speed control, making them a common type of inverter motor. The VFD adjusts the frequency of the power supplied to the motor to control its speed.
- Permanent Magnet Synchronous Motors (PMSM) with Inverters:
PMSM motors, which have permanent magnets in the rotor, can be used with inverters for variable speed control. In this setup, the inverter controls both the frequency and voltage to regulate the motor’s speed.
- Switched Reluctance Motors (SRM) with Inverters:
Switched Reluctance Motors can be operated with inverters to achieve variable speed control. The inverter adjusts the current flow to different motor phases, allowing precise control over the motor’s speed and torque.
- AC Motors with Sensorless Vector Control Inverters:
AC motors equipped with sensorless vector control inverters use advanced control algorithms to achieve precise control over speed and torque without the need for external position sensors.
Permanent Magnet Motor Manufacturer: Innotec Power
Innotec Power is the Manufacturer of Permanent Magnet based electric motors for Global OEMs. Our range of motors are designed to easily integrate and work with different VFDs (Variable frequency drive) and Inverters making them variable speed motors. All our Permanent Magnet motors are tuned with the VFDs in such a way that they deliver optimum performance as required by the on field task maintaining a balance between speed and torque output.
Working with Innotec, gives OEMs the opportunity to customize the mechanical and electrical features of the motor according to their torque requirements.Get in touch with us to discuss more about custom Inverter Motors.
Get in touch with us to discuss more about custom Permanent Magnet Motors. Check out our standard motor offerings:
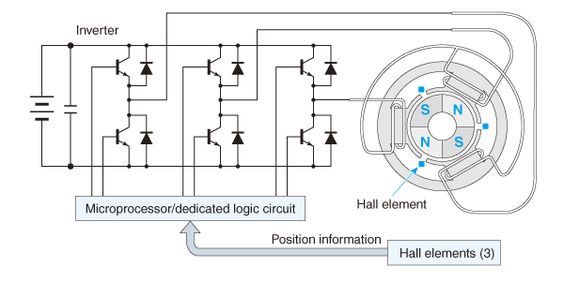
Choosing the Right Inverter Motor
Choosing the right inverter motor is a critical decision that depends on various factors, including the specific application requirements and operational conditions. Here’s a detailed guide on how to choose the right inverter motor:
- Understand Application Requirements:
- Identify Specific Needs: Clearly define the purpose of the motor. Determine whether it’s for industrial machinery, HVAC systems, appliances, or other applications.
- Load Characteristics: Analyze the load characteristics, such as torque requirements, duty cycle, and speed variations. Different applications may have distinct demands on motor performance.
- Motor Specifications:
- Power Rating: Consider the required power output in terms of kilowatts (kW). Ensure the motor’s power rating aligns with the application’s demands.
- Voltage and Current Ratings: Match the motor’s voltage and current ratings with the power supply specifications to ensure compatibility.
- Frame Size: Evaluate the physical dimensions of the motor, including the frame size, to ensure it fits into the designated space in the application.
- Operational Environment:
- Temperature and Humidity: Consider the environmental conditions where the motor will operate. Ensure the motor is designed to withstand the temperature and humidity levels in the application area.
- Enclosure Type: Choose an appropriate motor enclosure based on the environmental exposure. Options may include open drip-proof (ODP), totally enclosed fan-cooled (TEFC), or explosion-proof enclosures.
- Control and Feedback Mechanisms:
- Sensor Requirements: Determine whether the application requires sensorless control or if sensors (such as encoders or resolvers) are necessary for precise speed and position feedback.